CONCRETE SOLUTIONS FOR CONCRETE PROBLEMS
CASE STUDIES
The following case studies were successfully performed using The Rock Doctor's industry-standard services, techniques, and methodology for customers in real-world production situations.
- Low Strength Concrete
- Alkali-Silica Reaction Diagnosis/Remediation
- Air-entrained Concrete Receiving a Steel Trowel Finish
CASE STUDY #1: LOW STRENGTH CONCRETE
MATERIAL IN QUESTION: 80 yards of hardened concrete.
CUSTOMER: National Retailer.
REASON FOR REQUEST: Lower than intended compressive strength of affected concrete.
SYMPTOMS: 7 and 28-day cylinder and 28-day core breaks were 3,000 psi vs. intended 4,000 psi @ 28-days.
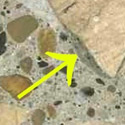
DIAGNOSIS: Concrete exhibited over 10% air content vs. specified 5%. Loss of compressive strength following the standard adage of For each 1% of air content in excess of intended amount, a loss of ultimate compressive strength of 3-5% should be expected. The excess 5% of air correlated well to a 25% loss of compressive strength (3,000 vs. 4,000 psi).
But why was the air content elevated? Petrographic examination showed distinct, discontinuous remnants of the original w:c ratio paste adhering to almost every coarse aggregate particle (click for detail, see yellow arrows). These remnants are described as veneers and showed markedly lower w:c, lower air content, lower water absorption, and greater resistance to scratching as compared to the bulk paste. Veneers are typical in retempered concrete. Retempering is the addition of excess water above and beyond the original mix design. After the customer received their report, it was discovered that a documented construction delay had occurred for over a two-hour period when these suspect 80 yards of concrete were placed. The ready mix trucks were lined up and waiting under 90°F temperatures. Under these conditions, the concrete (approximately 9 truckloads) had lost considerable slump. Large amounts of water were added to the trucks to regain slump and the concretes were placed without plastic air contents being taken.
RESULT: Based upon our report, the concrete was removed and replaced at no expense to the customer.
CASE STUDY #2: ALKALI-SILICA REACTION DIAGNOSIS/REMEDIATION
MATERIAL IN QUESTION: Concrete decking of a parking garage.
CUSTOMER: Major U.S. City Airport Authority.
REASON FOR REQUEST: Failure of initial repair attempts and further deterioration of concrete.
SYMPTOMS: Localized cracking and failure of previously repaired areas. Affected areas of were the south end of an elevated deck and the south end of the deck directly below.
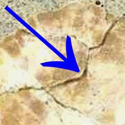
DIAGNOSIS: Concrete exhibited active alkali-silica reactions (ASR) associated with microcrystalline quartz chert particles in the coarse aggregate of the concrete. Chert varieties, phyllites, slates, metaquartzites, gneisses, schists, and other rocks containing low temperature silica/silicate minerals and/or strained quartz are potentially reactive with cement alkalis. The triangle of doom, composed of water, alkalis, and reactive aggregate(s) must be present for alkali-silica reactions to occur. If one of these components is not present, the reaction will not occur. Petrographic examination showed internally cracked, coarse aggregate particles with alkalic gel exudations (click for detail, see blue arrows) in representative concrete cores that showed distress/physical disruption. At a later jobsite survey, the affected areas were associated with water accumulations/poorly functioning water drainage areas. It was determined that critical saturation and continued exposure to water over the years predisposed these areas to undergo accelerated ASR vs. other unaffected areas with more slowly developing symptoms.
RESULT: Based upon our report, the poorly functioning drainage system was repaired, localized sections of affected concrete were isolated, removed, and replaced achieving significant cost savings and extending the service life of the parking garage.
CASE STUDY #3: AIR-ENTRAINED CONCRETE RECEIVING A STEEL TROWEL FINISH
MATERIAL IN QUESTION: Concrete with delaminating top surface.
CUSTOMER: Independent Ready Mix Producer.
REASON FOR REQUEST: Claim of alleged defective concrete supplied to job.
SYMPTOMS: Hollow sounds when chain dragged; cracking; loss of finished surface; thin delaminations.
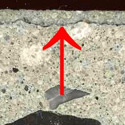
DIAGNOSIS: Concrete exhibited 6% air content that was specified and delivered as such. The problem was within the specification to have the floor slab receive a steel trowel finished surface. The weather forecast called for 1-2 weeks of unseasonably low temperatures with chances for rain/snow with drops in temperatures below freezing. The design engineer correctly assumed that newly placed concrete could be susceptible to freezing- while-plastic and/or freeze-thaw damage. He changed the mix design from a non- air entrained mixture to 5-7% air content concrete without informing the finishing crews. The difficulties encountered by attempting to finish air- entrained concrete with a steel trowel are well documented within our industry. Petrographic examination showed the characteristic 1/8 of an inch zone of air-detrained paste associated with steel trowel finishing effects (click for detail, see red arrows). Further examination showed the affected zone to have a markedly darker gray color as compared to the bulk paste. NOTE: Adjacent to the lost surface portion, incipient, or impending, delamination is likely to occur along the horizontal, subsurface fracture zone. These areas in the floor slab are the cause of the hollow chain drag sounds.
RESULT: Based upon our report, it was determined that the ready mix producer delivered the concrete as specified and was exhonerated from the case.
Please review our petrographic services or ask the doctor to see how our approach will work for you.